Non-combustible aluminium panels
ProClad™ SOLID high-quality aluminium panels are the ideal solution for any facade. The non-combustible panels come in a vast array of colours to suit a range of applications from high-rise commercial buildings to residential development.
ProClad™ SOLID is the perfect solution for any new build as well as recladding of existing projects. Architects, designers, developers, builders and contractors can feel confident when specifying ProClad™ SOLID aluminium panels as they are 100% non-combustible, require low maintenance and have a high level of safety and durability.
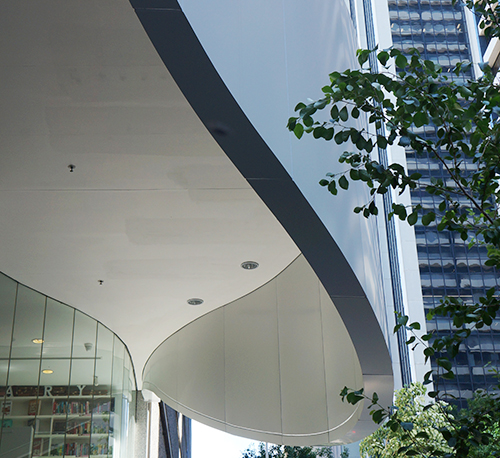
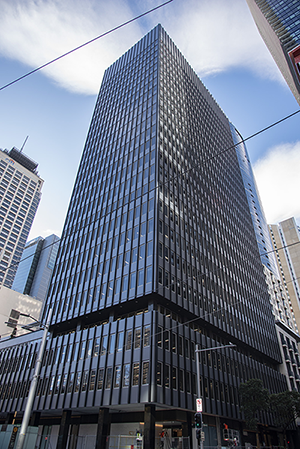
Designed to last
ProClad™ SOLID aluminium panels are non-combustible in accordance with AS1530.1 standards. The high-quality PVDF UV-resistant paint finish makes ProClad™ SOLID panels the ideal solution for harsh Australian conditions.
Regular cleaning with mild detergents is recommended. When cleaning the panels it is also recommended that the detergent is thoroughly rinsed off the facade to help maintain its original appearance.
Avoid using cleaning products that are highly alkaline or acidic as well as abrasive materials and paint dissolving solvents.
Facades that are located near a marine or industrial environment may need more frequent cleaning periods.
ProClad™ SOLID colour options
ProClad™ SOLID use global leaders PPG coil coatings, which include some of the industry’s best-known brands.
For nearly 50 years, DURANAR® coatings made with 70% fluoropolymer resin, have provided exceptional colour fastness, gloss retention and durability on buildings, including some of the world’s most recognised landmarks.
As a global leader in coil coating technologies, PPG offers products in multiple resin formulations to meet the colour, cost and performance demands of architects, building owners and building product manufacturers.
All PPG coil coatings are tested on chrome-pre-treated steel and aluminium using ASTM standards, so you can be confident that the coating you choose will perform to your expectations every time.
Colour representations on this website are for illustrative purposes only. You should request samples before placing your order.
Solid colour options
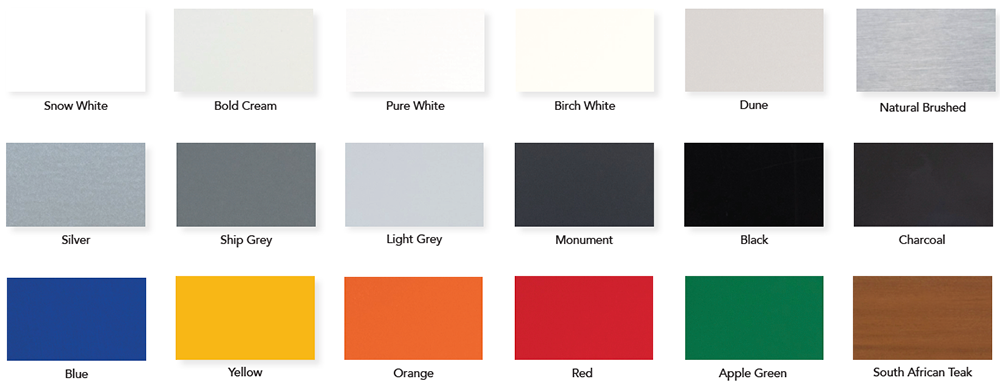
Metallic colour options
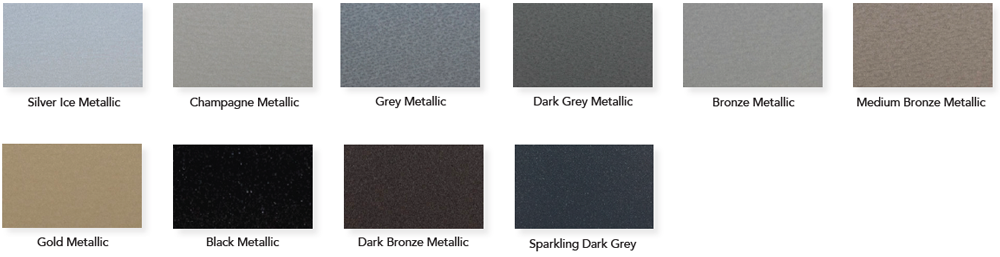
ProClad™ features and benefits
Designed to last
ProClad™ products are non-combustible in accordance with AS1530.1 standards.
The high-quality PVDF UV-resistant paint finish makes ProClad™ SOLID panels the ideal solution for harsh Australian conditions.
A range to suit any design
The wide range of finishes and sizes means that ProClad™ products can be used to achieve even the most complex architectural designs.
Standard sizes and colours are stocked in Australia for added convenience. ProClad™ also offers custom colours and sizes on request.
Non-combustible
ProClad™ is the perfect solution for any new constructions as well as recladding of existing projects.
Architects, designers, developers, builders and contractors can feel confident when specifying ProClad™ products as they are 100% non-combustible, requires low maintenance and have a high level of safety and durability.
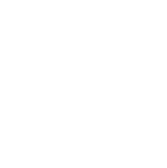
Perforating
ProClad™ SOLID sheets can be perforated by punching, drilling or milling.

Welding
TIG and MIG welding are common welding methods used on ProClad™ SOLID sheets.
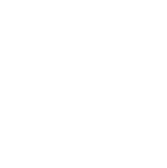
Perforating
Blind and solid rivets along with Stainless steel screws can be used to secure ProClad™ SOLID sheets.
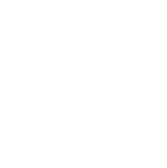
Drilling
A high-quality HSS centre point drill bit is suitable for drilling ProClad™ SOLID.
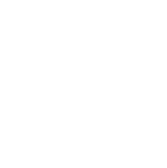
Roll Bending
To create curved surfaces, use a suitable bending machine. In order to minimise damaging the material use a protective film.
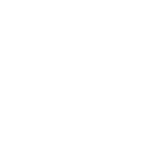
Shearing
ProClad™ SOLID sheets can be guillotined to the required size.
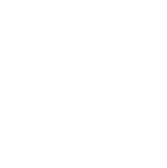
Folding
After the V groove is formed, fold the return leg in one movement. A portable folding tool for small panels and a folding machine for larger panels are recommended.
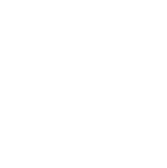
CNC Router
Used for straight and contour cutting along with V Grooving for folding. When creating a V groove for folding the minimum thickness left in the bottom should be 0.7mm.
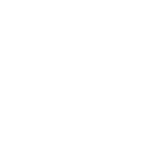
Vertical Panel Saw
Use for cutting and routing sheets. When creating a V groove for folding, the minimum thickness left in the bottom of the groove should be 0.7mm
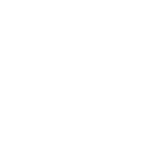
Circular Saw
For best results, a track-guided circular saw is recommended. Hand folding is achievable without a requirement for bending equipment.